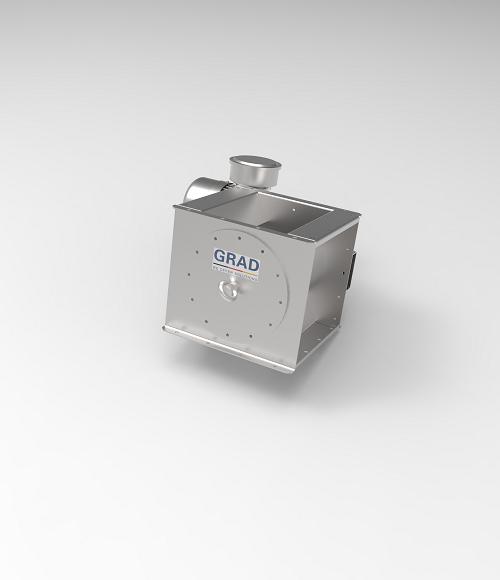
Rotary valves are used to discharge dust, chipboard shavings and fibrous conveyed goods, and as shut-off devices. A range of designs are available to suit various requirements, with throughput volumes to accommodate every case.
Grad rotary valves can also be delivered as type-tested protective systems (resistant to ignition and flame penetration) for explosion decoupling purposes.
When it comes to ensuring availability and operational safety in dedusting plants, discharge and conveying mechanisms are just as crucial as fans and filter systems. Extraction, filtration and material discharge devices thus form a single unit.
For free-flowing dusts with both hard and fine graining
Design: casing made from grey cast iron, with optional hard chrome-plated casing bore, full-blade rotor as standard in grey cast iron or made from wear-resistant steel
Throughput volume: 1.5 to 30 m³/h
The discharge falls from the hopper into the rotary airlock. Paddle wheels with rubber extensions to keep the system hermetically sealed collect the discharge. A motor drive rotates the paddle wheels at a specified speed and eventually the particles are evacuated from the bottom of the system without breaking the air seal.
These units come complete with a TEFC motor (575/480/240V), all gears, covers, flaps, chain, gearbox, support, and protective guard. Standard sizes are 6”, 10”, 15” & 20”. Capacities range from 20 to 104 cubic feet per minute.
Standard sizes of 6'', 10”, 15'' and 20”
Mild steel industrial construction
TEFC motor (575/480/240V)
Gearbox, chain and OSHA protective guard
Neoprene rubber seals
Inlet/outlet boltable flange
Stainless steel components
Silicon type rubber seals
Explosion proof motor
Anti-abrasion steel casing
Zero speed switch (rotation sensor)
Product density
Abrasion
Temperature
Process ∆P
Product discharge rate
Available voltage